What is the Procedure for Testing the Pull-Off Strength of Air Barrier Materials?
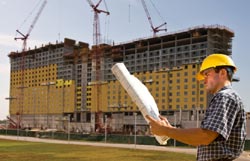
What is the Procedure for Testing the Pull-Off Strength of Air Barrier Materials?
The National Air Barrier Association (NABA) requires adhesion (and cohesion testing on SPF) testing (commonly referred to as pull testing) to be conducted in the field in accordance with ASTM D4541 on all jobs that are specified under the NABA QAP that use fluid-applied, self-adhered and spray polyurethane foam (SPF). See NABA Daily Work Sheets and NABA Audit Forms for the number of discs that are required. The purpose of this test is to measure the adhesive strength of a material to determine whether the installation has been completed correctly. Release or separation during the test will occur along the weakest part of the material, or bond between the material and the substrate. This could include the interface between the test apparatus and material, between two materials, within the material, between the substrate and the material, or between the surface of the substrate and the substrate.
Poor adhesion can be the result of improper substrate preparation, the adhesive surface of the material becoming contaminated with water, dirt, oil or grease, improper primer application which includes too little, too much, not properly cured, and in the case of some materials- not being rolled with a membrane roller. In short, if adhesion is used to keep the air barrier in place and to withstand the wind, stack, and mechanical pressures over the service life of the building, the air barrier material requires the proper adhesion. Each material will have a different adhesion value, and this value will change depending on the substrate the material is installed on.
The most common cause of failure is a low/high pressure on the material over a long period of time. To determine whether proper adhesion has been achieved, on site testing needs to be conducted. The basic principle is very simple- attach a 2¼" to 4" steel or plywood disc to the air barrier material, cut around the material so you are pulling on a specific area of the material to not damage more material around the area of the test.
Read the instructions for operating the adhesion tester prior to commencing the test. Ensure the adhesion tester has the range of expected values- if you overload the tester, you will destroy the gauges. When attaching the adhesion tester to the pad adhered to the air barrier material, ensure that the specimen is not being pre-stressed by bumping or bending. For non-horizontal surfaces, support the adhesion tester so its weight is not added to the force exerted on the sample.
To reduce the risk of separation between the material and the equipment, the surface of the material can be lightly abraded to remove any surface film that could interfere with the adhesion to the material. If the surface is abraded, care must be taken to prevent damage to the air barrier material or significant loss of material thickness. Clean the abraded areas with a manufacturer-approved cleaning agent to remove any particulates after abrading. It is important to select a cleaning agent that does not affect the integrity of the material or leave a residue. Clean the pad surface of the equipment as indicated by the manufacturer to avoid separation of the equipment from the material during testing.
Before you conduct a pull test, ensure that the air barrier material being tested has properly cured according to the manufacturer's specifications. The material that is being tested must be flat for proper adhesion of the disc. In the case of SPF, the foam can be trimmed with a knife so that the pad is flush and bonds properly.
Ensure the epoxy being used states on the package it will bond to plastic (for fluid-applied, self-adhered or SPF materials) or metal (for foil-faced materials). If you are using a two-part epoxy, prepare the epoxy in a separate container or on a separate surface, not on the face of the pad. Apply the adhesive to the pad and the surface of the air barrier material in accordance with the adhesive manufacturer's instructions, removing any excess adhesive from the sides of the pad. Allow the adhesive to cure for a time in accordance with the adhesive manufacturer's instructions.
Once the pad is placed on the air barrier material, do not twist or move it as it can dislodge the pad and result in incorrect values during testing. During the initial cure of the adhesive, apply a constant pressure to the pad using either your hands, or a clamping system. Care should be taken when using tape to hold the pad in place to ensure that the entire pad is completely pressed against the substrate.
If a bearing ring is required for the test, place the bearing ring around the pad on the air barrier material surface so that the adhesion tester is equally supported. If shims are required to level the bearing ring, place them between the base of the tester and bearing ring.
When applying the force to the pad, ensure that the force is applied in a smooth, continuous and even manner to achieve a uniform pulling force. Force increases must be steady and incremental within the rates specified in ASTM D4541, method B. If a steady rate of applying the force is not followed, the area where the force is concentrated will cause that portion of the material to separate long before maximum stress has been reached, and the test result will be invalid. The force shall be applied to the pad by turning the handle not be more than one revolution per minute (rpm). The gauge will display the force being applied and the limit stop dial will register the peak force just before there is a separation.
Note: Weather and substrate conditions during the test can affect the pull-off force values. Do not perform the test in direct sunlight as this will cause skewed values.
Once the tests have been completed and the fixture has been removed from the pad, the specimens shall be analyzed. The maximum force achieved, the type of release, the surface in which the release occurred and the percentage of release on each surface should be noted in the test report. The value from the test shall be reported on the daily work sheets and audit reports in lbs from the gauge. A formula in Section 8 of ASTM D4541 can be used to calculate the greatest pull-off stress applied during a test in psi.
If an anomaly in test results is found, this anomaly should be investigated to find the cause. If it is determined that the cause is from improper test procedures, the value shall not be included in the results and another test will have to be performed.
Air barrier material that was damaged by the pull test shall be repaired in accordance with manufacturer's instructions.
The gauge of the test equipment must be calibrated to guidelines acceptable to the test equipment manufacturer. See the recalibration instructions when replacing gauges.