Quality Assurance Program
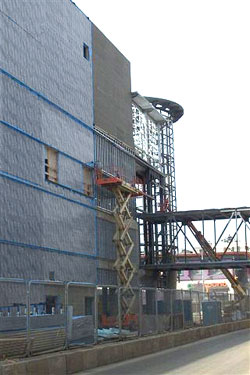
The Quality Assurance Program is based on nine main components. All these components interact with each other and the association has found that the quality of the program can't be based on one single component--but rather with all nine components.
RESEARCH AND DEVELOPMENT
Proper research into installation practices, product performance, design considerations, and the compatibility of different air barrier materials are all important parts of NABA's research and development. This component is on-going as products and installation practices change.
STANDARDS AND SPECIFICATIONS
Standards and specifications deal with both the air barrier products and installation. For air barrier products, a national standard is established to provide a benchmark for suppliers. This standard for the product details the testing requirements and results needed for materials to be deemed an air barrier.
The standard for installation provides a benchmark for the insulation of different materials, on-site testing requirements, and guidelines for such things as substrate preparation, and application temperatures.
LICENSING/ACCREDITATION OF MANUFACTURERS
The manufacturer agrees to produce a product that meets the standard and signs a licensing agreement outlining the responsibilities.
LICENSING/ACCREDITATION OF CONTRACTORS
Contractors are required to employ a certified installer, have set amounts of general liability insurance, must be bondable up to a determined amount, abide by the association ethics and guidelines, and sign a licensing agreement dictating professional conduct. The contractor is identified as the legal identity and the one responsible for the application of the air barrier system.
CERTIFICATION OF INSTALLERS
Installers are required to be trained and certified.
Installers are require to sign a licensing agreement outlining their requirements. Installers are responsible for the professional application of air barrier systems, daily on-site testing, documentation, and providing a safe work environment. This component is regarded as one of the most important pieces of the system.
FIELD AUDITS
As part of the Quality Assurance Program (QAP), each NABA-specified project has third-party audits of the installers work. The number of audits conducted shall be either how many the specifier has specified or the number as per the NABA QAP and listed in the NABA master specifications. The auditor will conduct a visual and physical examination of the air barrier installation to ensure all aspects of the air barrier installation including the conformance to the project specifications and to ensure the air barrier materials and accessories are installed as per manufacturers specifications. The auditor shall ask to see the Daily Job Site Reports for that day and for days prior to the audit. The auditor will verify that the information recorded on the form is accurate and complete to the extent that this can be done.
Once the NABA auditor and the NABA QAP technical staff have reviewed the audit report, it and accompanying pictures are sent to the Air Barrier Contractor, General Contractor, Architect (specifier) and Manufacturer. This allows for the interested parties to resolve any concerns that have been found during the audit.
Click here for a sample of a self-adhered audit form that the parties noted shall receive.
DOCUMENTATION
Installers are required to perform daily testing to confirm quality of insulation. All testing results, substrate preparation, identification of work force, and other information is documented on a daily work sheets and start-up sheets. All work sheets are kept on file at the NABA office and the contractor's office.
DATABASE TRACKING
A database has been set up monitor the program. All contractors, installers, manufacturers, and field audits are centrally data based. This data base keeps track of installer and contractor demerit points, results of the field audits, and problems with certain materials or applications. The system provides feedback to the manufacturers, contractors, and installers and identifies problems.
APPEAL PROCESS
A process is in place in which the contractor or installer may initiate an appeal process in the case where the contractor or installer license is revoked. The process contains three levels in which the contractor or installer may appeal any decision made by the certification body. The appeal process is handled by a third party.